

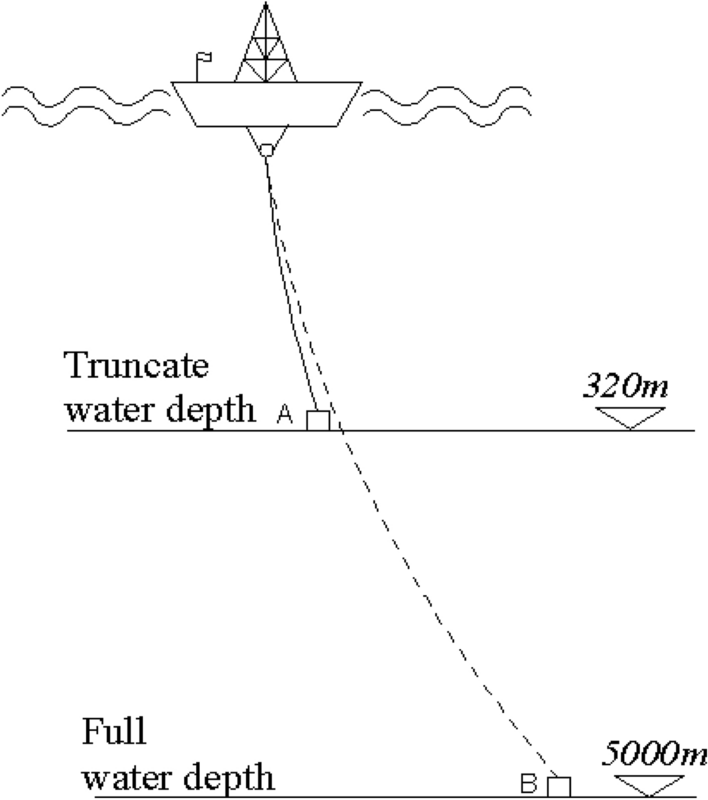
set the float properties(name,category,OD,ID,length,pitch,drag coefficients.create a section along the length of the pipe.set the position and orientation of each End.Connect EndA to vessel and anchore EndB to seabed.this project uses default Orcaflex vesselRAO, for real life project, the typical vessel FPSO RAO will be used.set the vessel position (translation and rotation).set the vessel length,type and end boundary connection.variable drag coefficient as a function of Reynolds number.set variable current values at corresponding water depths.wave type, wave direction,significant waveheight,and peak period.stagecount, stagedurations and number of iterations.import OrcFxAPI - OrcFxAPI is the Python-orcaflex API.The maximum combined load unity checks due to combined effect of effective tension, bending moment and pressure effects are also automatically extracted from the analysis.
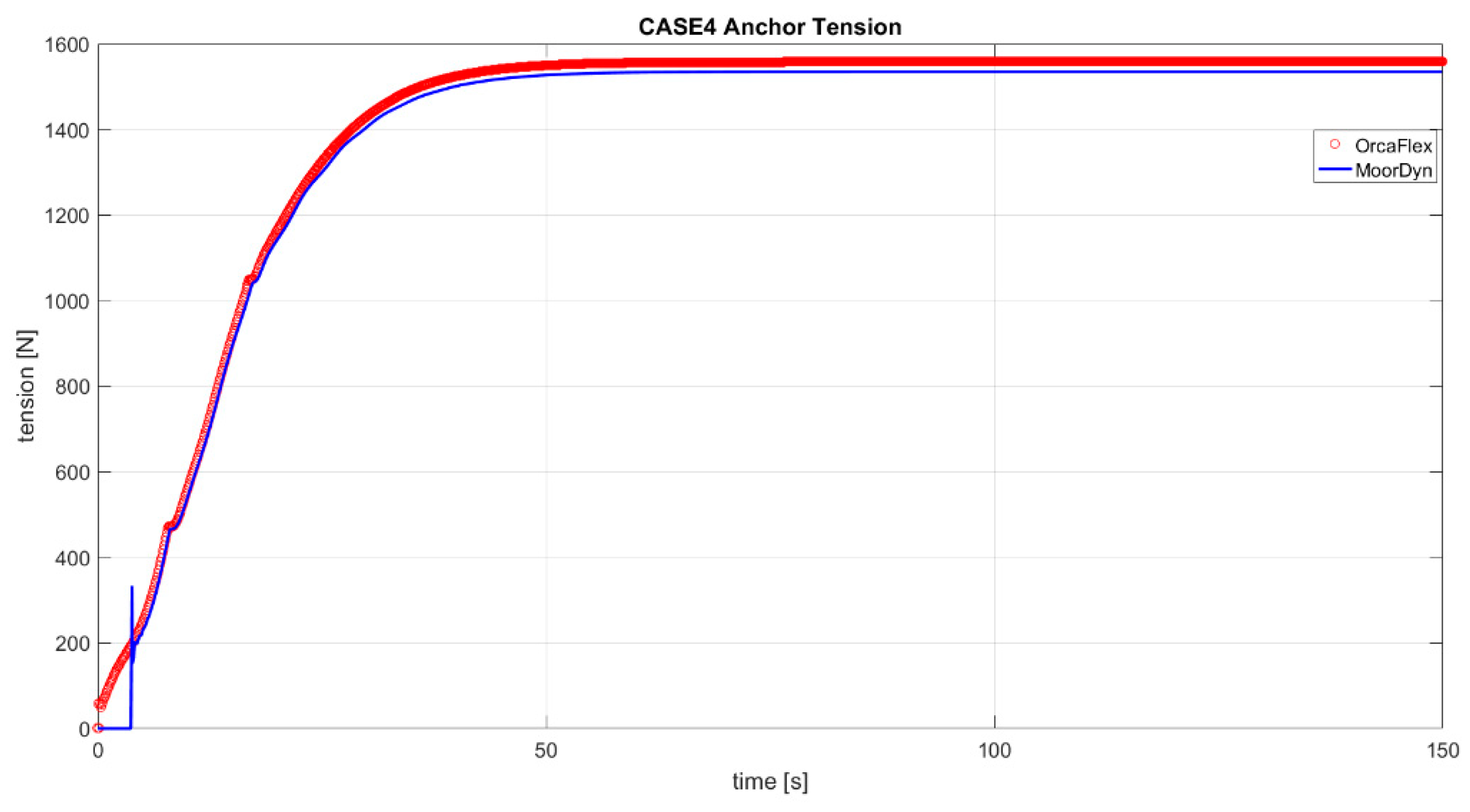
The analysis results are compared to the allowable limits to determine if the response is acceptable or not. The allowable limits for effective tension, stresses, are computed from DNVOSF201 recommended practice taking into consideration the LRFD methodology, design factors and material strength. The response of the riser due to hydrodynamics loading(wave,current), vessel RAOs, pipe self waight and content are simulated to determine the worst values for effective tension(top and bottom), bending moment, stresses, maximum combined loading on the riser. The EndA is connected to FPSO at the topside and EndB anchored to the seabed. The riser is similar to a catenary riser but with a distribued buoyancy module placed along a section of the riser to form a lazy configuration. The entire process from preprocessing to postprocessing was automated in Python.This method can also be applied to umbilicals, hoses.

This project involves building an analysis tool with ORCAFLEX-Python API to automate subsea lazywave riser modelling, analysis and postprocessing. Lazy wave riser analysis automation tool.
